Stretching Solder Capabilities
Solder paste dispensing can solve the challenges posed by differing component sizes.
by Timothy O’Neill
While stencil printing has long been the cornerstone of applying solder paste, it faces limitations with extremely small or large components. This challenge underscores the need for adaptable and innovative solder paste application methods. Here we delve into the realm of advanced dispensing technologies, exploring solutions that can help overcome common production challenges.
Stencil printing, despite its efficiency, struggles with the dual extremes of component sizes – area array and bottom termination components continue to shrink, while connectors and other components may increase in size. This variance stretches the capabilities of stencil printing. Dispensing offers the advantage of infinite flexibility, capable of producing both minuscule and substantial deposits while seamlessly integrating into the existing SMT process.
For example, a 25-gauge dispensing needle has an inner diameter of 10 mils, or 0.25mm, and a length of 0.25″, or 6.35mm. If that tip were treated as a stencil aperture and its area ratio calculated, it would be 0.10, which is considered impossible on a stencil by a factor of five! Without the pressure of the dispenser and finer solder particles in the paste, nothing would get deposited onto the PCB. Figure 1 shows a typical 25-gauge needle producing a 15-mil, or 0.375mm, deposit with Type 6 solder paste.
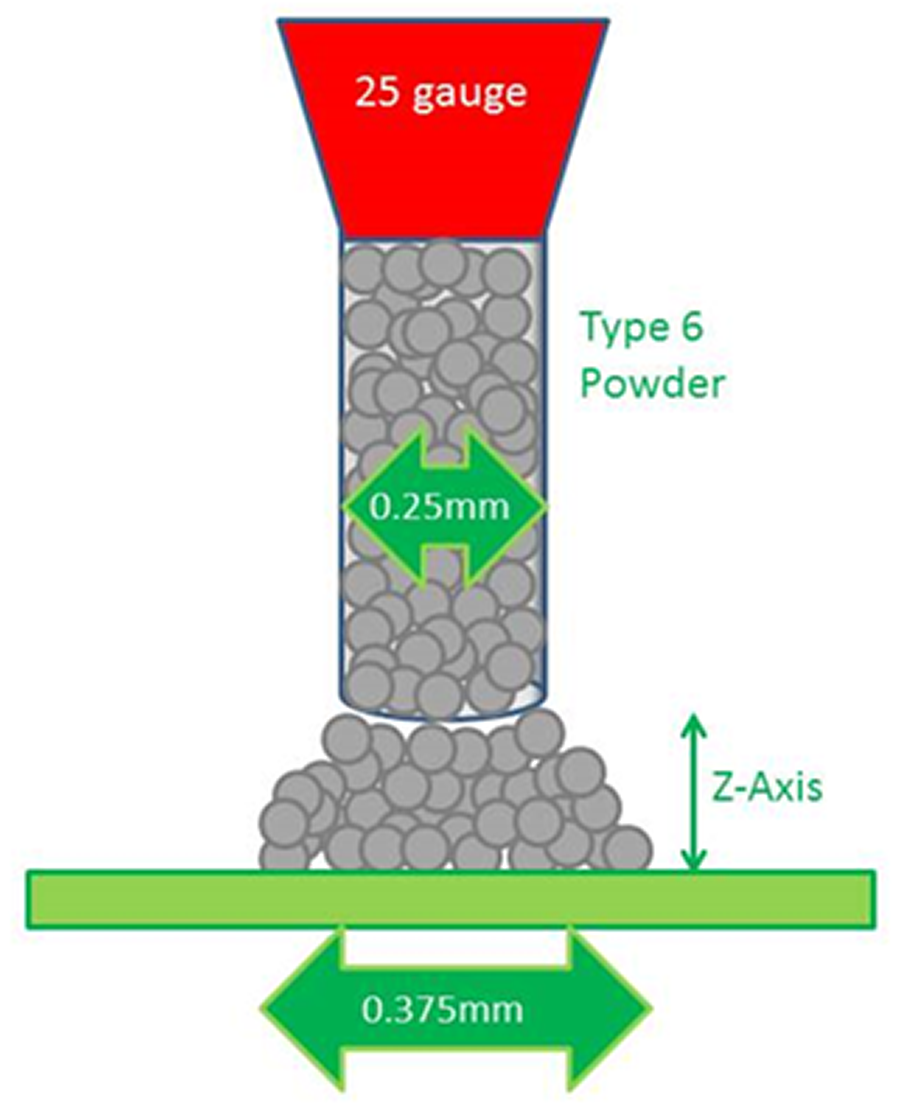
Dispensing techniques. Dispensing technology encompasses several methods, each with its unique advantages and limitations. Table 1 summarizes the advantages and disadvantages of three main classes of dispensing equipment used for solder paste deposition.
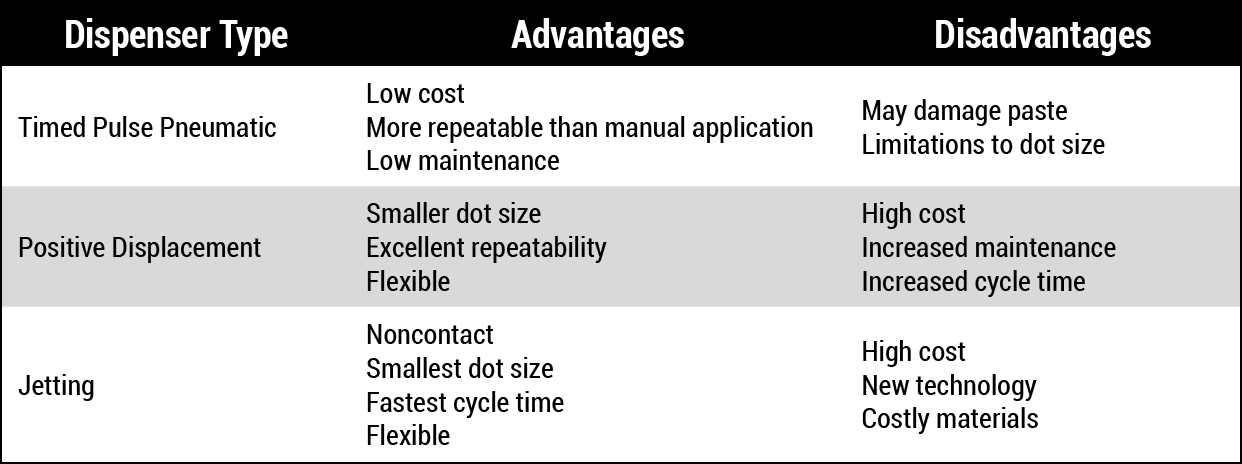
Despite the apparent benefits, dispensing’s primary drawback is its cycle time, which is significantly slower compared to the thousands of deposits a squeegee can achieve in one stroke during stencil printing. When substrate or component configuration and solder paste volume requirements do not permit stencil printing, however, dispensing solder paste may be the best option, either by itself or in addition to printing. Some stencil printer models even have internal paste (and adhesive) dispensers as an option, as seen in Figure 2.
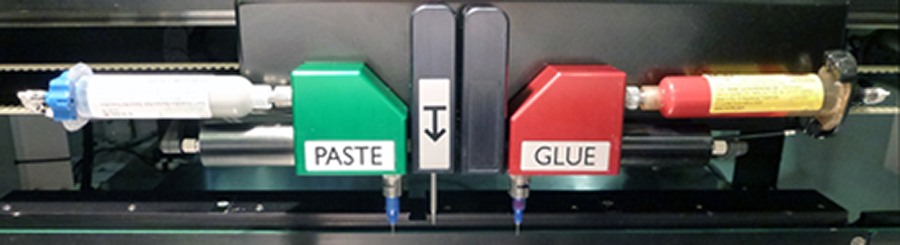
Optimizing dispensing for efficiency and quality. Achieving success with dispensing technologies requires careful consideration of equipment selection and process adjustments. The solder paste being dispensed consists of two primary ingredients: solder alloy powder and flux medium. Because solder and flux densities are so different, keeping the suspension homogenous during dispensing is challenging.
Additionally, solder powder is particulate material, which increases the probability that dispensers will occasionally clog. To avoid separation or clogging with timed pulse pneumatic and positive displacement dispensers, several key guidelines should be carefully followed:
- Use the shortest tip length possible.
- Keep air pressure as low as possible; <40psi (2.75bar) for timed pulse dispensing and for <10psi (0.7bar) positive displacement, and do not cycle the air pressure on/off.
- Control the z-axis height relative to the substrate. This is critical for dot-to-dot size repeatability and reproducibility.
- Store solder paste under refrigeration, tip down, before use. If warmed to ambient temperature, do not re-refrigerate.
- Once paste has begun clogging the dispense tip, it should be scrapped.
Modifications in powder mesh size and metal content may also be necessary as the dispensing tip’s inner diameter decreases, necessitating collaboration with material suppliers to ensure compatibility and performance.
Solder paste jetting advancements. Solder paste jetting has gained popularity due to its flexibility and precision, permitting easy adjustments in paste deposit locations and volumes. The latest jetting technology has not quite matched the speed of printing but has narrowed the gap considerably in comparison to its predecessors. For high-mix/low-volume or prototype manufacturers, it is a technology worth investigating.
Additionally, paste jetting valves are now being fitted to solder paste inspection equipment to provide assemblers with a “no-touch” corrective method for addressing insufficient paste deposits identified by the SPI system (Figure 3). Paste can also be jetted onto PCB features requiring additional solder paste, potentially eliminating the need for stepped stencils, expensive preforms, or unconventional print techniques.
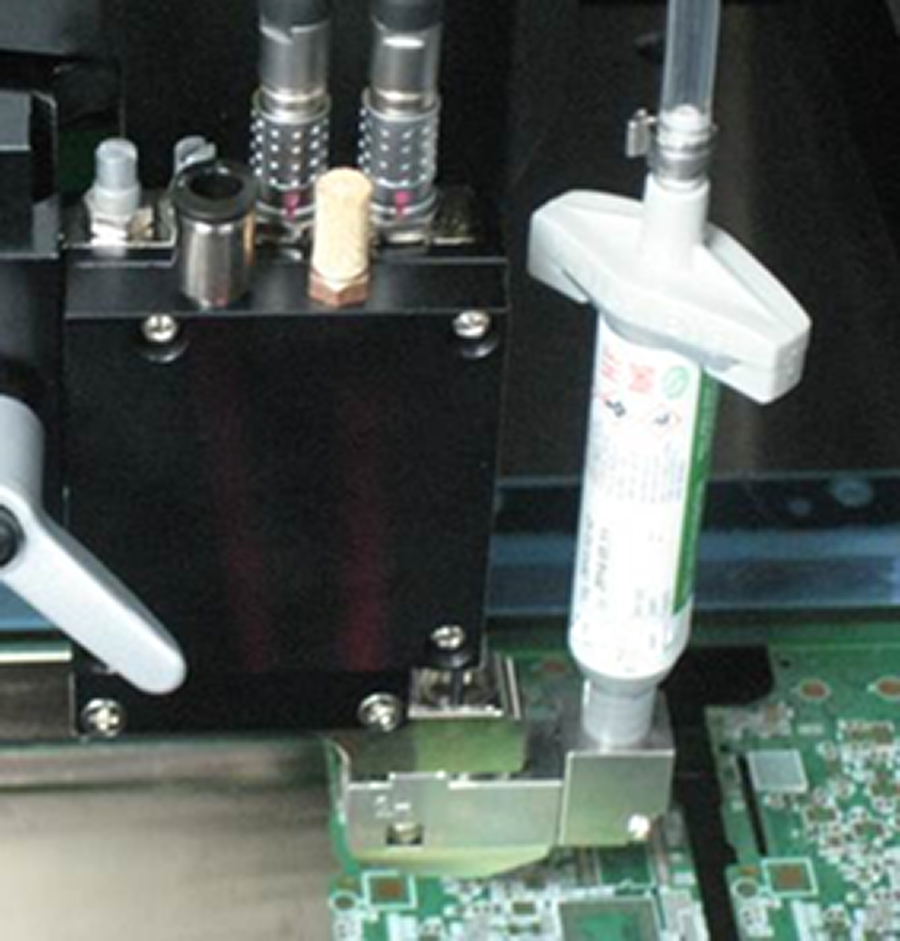
Strategic considerations for dispensing success. When it comes to solder paste deposition, stencil printing is almost always the first choice because it is the industry standard. Material availability and a vast resource and knowledge base within the technical community also make printing the preferred option. But when printing alone cannot supply small enough or large enough amounts of solder paste, dispensing is often the answer.
Critical to the success of dispensing methods is collaboration among assemblers, material suppliers and equipment manufacturers. Understanding the inherent properties of solder paste and the technical nuances of dispensing equipment can significantly impact the efficiency and quality of PCB assembly processes.
Timothy O’Neill is director of product management at AIM Solder (aimsolder.com); toneill@aimsolder.com