Flexible Heater with Non-Heating Leads
Three methods for incorporating non-heating leads into a heater pattern.
A flexible heater is needed where Constantan or Inconel is used for the heating area. Is there a way to incorporate a resistive layer into a standard flex circuit to have non-heating (copper) leads going to the heater pattern?
Answer: Yes, this is a common request and can certainly be done. Several methods are used to accomplish this, with limitations. A couple of these methods require selective plating of copper onto the resistive alloy element traces to lower the resistance, or using plated vias on other layers to make the non-heating connections. This works well on copper/nickel alloys like CuNi 715 or Constantan, but not so much so on Inconel 600 (these are the three most common resistive alloys used in flexible heater construction). The Inconel restriction is covered in more depth later in this column.
The first method requires three total layers in the stackup, with the internal layer the resistive (heating) layer. The outer layers are standard copper and include the traces feeding the heater along with any other circuitry you wish to include. Top and bottom copper layers are needed even if there are only the two heater leads and/or a couple of thermistor leads. In many cases, one of the outer layers will be only pads. Reason: To connect the heater element to a copper layer with a via, the entire panel must be electroless copper-plated to metalize the vias for electrolytic copper plating. If one of the outer layers is the resistive foil, that layer will now have a layer of copper plating that will significantly lower the overall resistivity of the element – making it non-heating. By burying the resistive element between copper layers, the element will receive copper plating in the via areas only.
The second method starts with a single layer of resistive foil, and then selective traces are copper-plated in areas you do not want heat generated (FIGURE 1). The one stipulation is that this can be done only on applications where the heater is a copper/nickel alloy like CuNi 715 or Constantan (i.e., not Inconel). The reason is copper-nickel alloys are very easy to plate with copper, and the bond between CuNi and copper plating is very good. Inconel, on the other hand, is relatively easy to copper plate, but the bond between Inconel and plated copper is very poor. The result is similar to plating copper onto stainless steel. In many cases the plated copper will peel off the Inconel before it can be locked in place with a polyimide cover. One potential workaround is to drill several holes along non-heating traces, then plate pads on the back side around each of the drilled holes, which effectively creates rivets, in addition to copper plating the trace on the top side. This does not improve the bond between the copper plating and Inconel, but will in most cases keep the plating in place until cover lamination locks everything in place. For this to be effective, the plated through-hole “rivets” need to be relatively close together, which can cause mechanical issues if the heater must be bent in the non-heated lead area (which is pretty common).
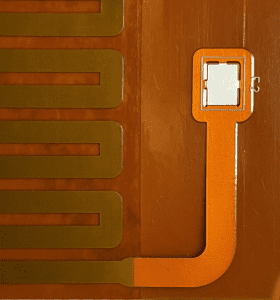
Overall, it is better to just increase the trace width of non-heating Inconel leads as much as possible and bypass the copper plating. Doubling or tripling (or more) the width of the traces you do not want to heat can reduce the heat generated in those traces by 50% to 75% or more. If real estate is not available to significantly increase the trace width of the heater leads, I recommend looking at using a thinner CuNi alloy with smaller traces to get similar overall resistance to Inconel. Again, it is a simple matter to then copper-plate the heater leads to keep them cool.
The last method for creating a flexible heater with non-heating leads is to build a standard flexible heater and a standard copper flex, and then connect the two using eyelets, conductive adhesive, etc. This can be done on CuNi alloy and Inconel-based heaters, and is typically considered when the size or shape of the overall heater/lead assembly results in extremely poor processing panel density. Significant improvement in panel density of both the heater and flex is common if they are built as separate items. While there will be an increase in assembly costs over selective copper plating, in some cases the material savings will result in lower overall cost of the flexible heater assembly.
Mark Finstad is director of engineering at Flexible Circuit Technologies (flexiblecircuit.com); mark.finstad@flexiblecircuit.com. He and co-“Flexpert” Nick Koop (nick.koop@ttmtech.com) welcome your suggestions.