A Journey in Rigid-Flex Design
Overcoming the challenges of rigid-flex designs can be incredibly rewarding.
As technology continues to advance, the demand for smaller, lighter and more efficient electronic devices is ever increasing. This demand has led to the emergence of rigid-flex PCBs, a revolutionary technology that combines the benefits of rigid and flexible circuits into a single solution.
As a principal PCB designer with several decades of experience in designing a wide spectrum of PCB technologies, I’ve had the privilege of delving deep into the world of rigid-flex PCB design. This month I’ll share insights and experiences from my journey within this fascinating technology.
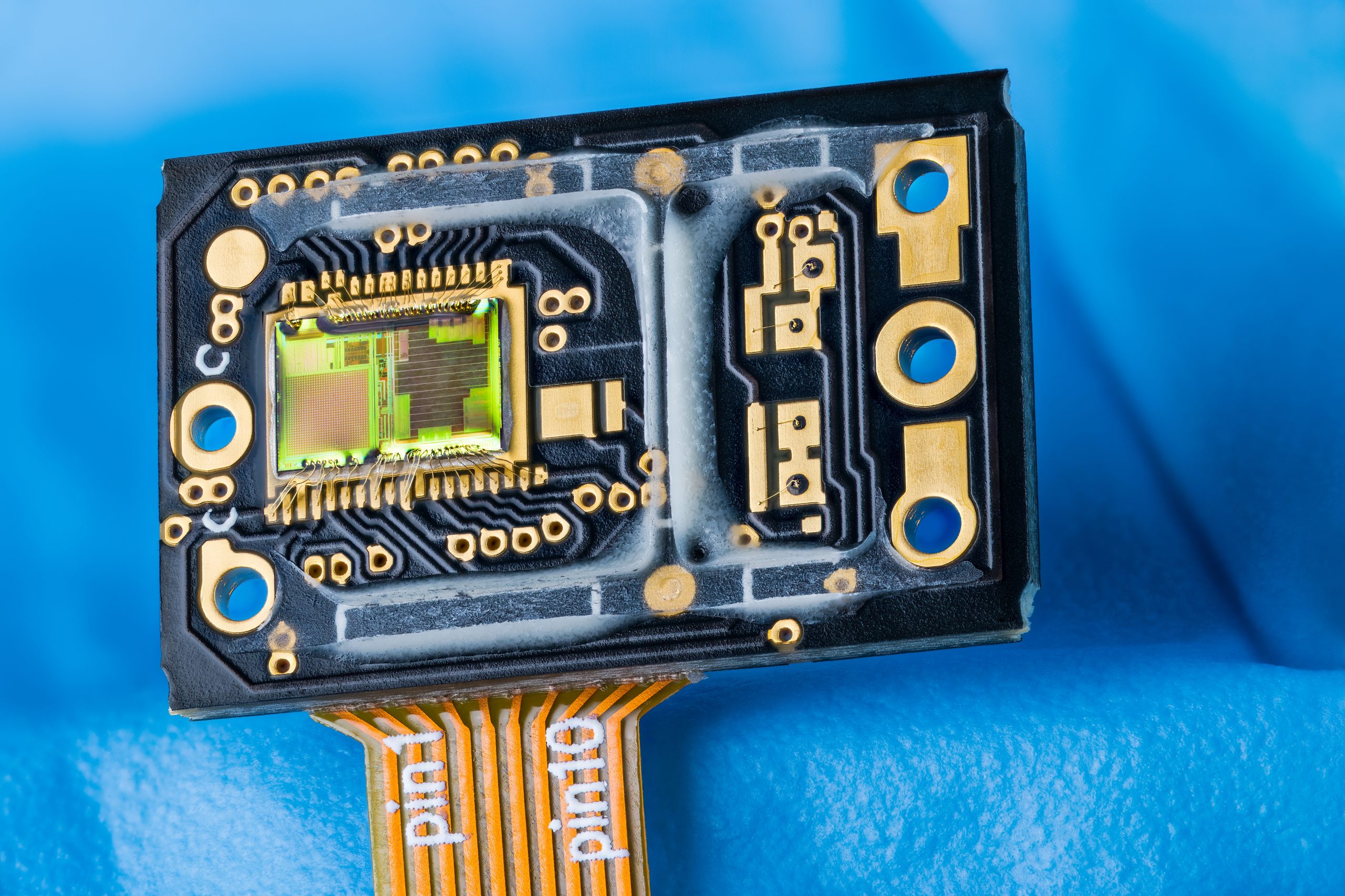
As I have progressed in my evolution as a PCB designer, more specifically with regards to rigid-flex PCB design, this technology has always presented a unique set of challenges and opportunities compared to traditional rigid PCBs or flexible PCBs. One of the significant advantages of rigid-flex technology is its ability to reduce space and weight in electronic devices while improving reliability and durability. Achieving these benefits, however, requires a thorough understanding of rigid and flexible circuit design principles, as well as the nuances of integrating them seamlessly.
In my early years at my first attempt with a rigid-flex PCB design, the thought alone intimidated me. Back then, rigid-flex PCB was kind of like a mystical type thing that was not widely understood. Even with several years of rigid PCB designs under my belt, I hesitated due to lack of knowledge in this realm but knew enough to get the fabricator involved at the earliest stages of design. Finding educational content on rigid-flex PCB design back then was not so easy. Not like it is today! Plus, EDA tools have come a long way and today have far superior capabilities and functionalities to address all the required details and constraints that make up a rigid-flex PCB design.
Here are some aspects to keep in mind.
Ensure mechanical reliability. Aside from collaborating with the PCB fabricator from the beginning of the project, one of the key considerations in rigid-flex PCB design is ensuring proper mechanical reliability. Unlike rigid boards, flexible circuits are susceptible to bending and twisting, which can lead to mechanical stress and fatigue over time. As a result, careful attention must be paid to factors such as material selection, bend radius and reinforcement techniques to ensure the reliability and longevity of the final product.
Manage signal integrity. Another challenge I have experienced in rigid-flex PCB design is managing signal integrity and impedance control. The flexible portions of the board introduce additional impedance variations and signal losses compared to rigid sections, which can affect the performance of high-speed and high-frequency circuits. To address this, designers must carefully analyze signal paths, use appropriate routing techniques and employ impedance matching strategies to maintain signal integrity across the entire board.
Design for manufacturability. In addition to mechanical and electrical considerations, rigid-flex PCB design also requires careful attention to manufacturability and assembly. Design for manufacturability is key. The unique construction of rigid-flex boards introduces complexities in terms of fabrication and assembly processes, which can impact yield, cost and time-to-market. Working closely with manufacturers and assemblers is essential to ensure that the design meets all requirements, performs as intended and can be efficiently produced and assembled with the highest yield and at the lowest cost.
Despite the challenges, working on rigid-flex PCB designs can be incredibly rewarding. The ability to create compact, lightweight, and highly reliable electronic products opens a world of possibilities for innovation and advancement. Whether it’s designing wearable devices, medical implants or aerospace systems, rigid-flex technology offers unparalleled flexibility and versatility for a wide range of applications.
Over the years, I’ve had the privilege of working on numerous rigid-flex PCB projects, each presenting its own set of unique challenges and opportunities. From designing intricate multilayer circuits to optimizing layouts for maximum reliability and performance, every project has been a learning experience that has helped me grow and evolve as a designer.
Rigid-flex PCB design represents the future of electronics engineering, offering a compelling combination of performance, reliability and flexibility. Today, as a printed circuit engineer, I feel fortunate to be part of this exciting journey, pushing the boundaries of what’s possible and helping to shape the future of technology. With continued innovation and collaboration, the potential of rigid-flex technology is limitless, and I look forward to seeing where it takes us next.
Ed: This column originally appeared in Siemens’ Electronic Systems Design blog.
Stephen Chavez is a senior printed circuit engineer with three decades’ experience. In his current role as a senior product marketing manager with Siemens EDA, his focus is on developing methodologies that assist customers in adopting a strategy for resilience and integrating the design-to-source Intelligence insights from Supplyframe into design for resilience. He is an IPC Certified Master Instructor Trainer (MIT) for PCB design, IPC CID+, and a Certified Printed Circuit Designer (CPCD). He is chairman of the Printed Circuit Engineering Association (PCEA); stephen.chavez@siemens.com. He will speak at PCB East in the Boston suburbs in June.