Preserving Solder Paste Integrity
A closer look at mixing methods and automated mixers.
by Gayle Towell
While automation in manufacturing brings efficiency and consistency, the use of automated solder paste mixers is a topic of debate, with significant concerns over their impact on the paste’s properties. This comprehensive analysis delves into why many industry experts advise caution.
Solder paste is not just a blend of materials; it’s a finely tuned compound where each element plays a specific role. The balance between solder powder and flux is crucial, as it determines the paste’s behavior during the printing process and affects the quality and reliability of solder joints. Certain properties of the paste – its viscosity, rheology and thixotropy – fundamentally determine how well it will perform and can be significantly affected by how the paste is handled.
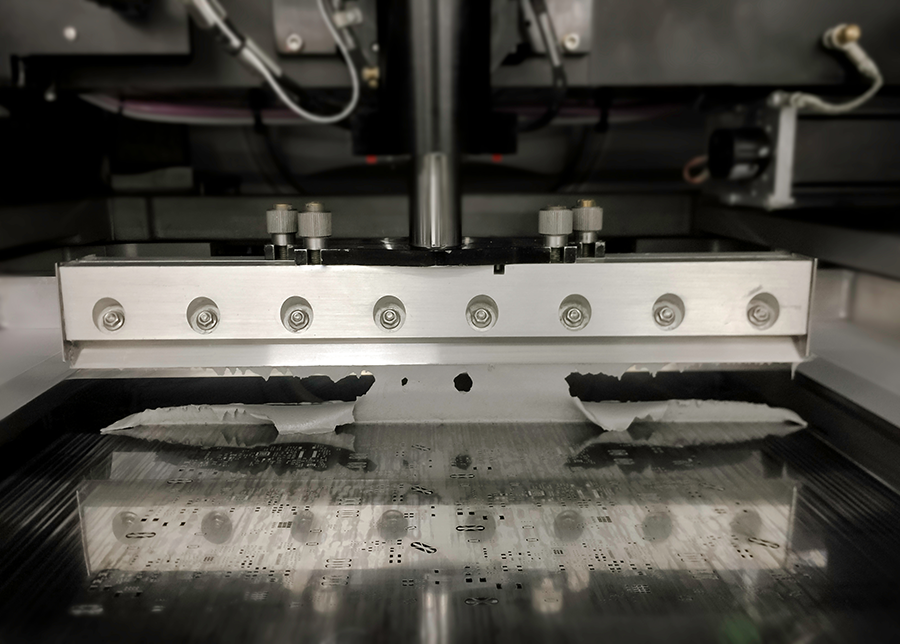
In solder printing, the right viscosity ensures the paste can be deposited accurately without spreading. Rheology involves the study of the flow and deformation of the paste and is essential for understanding how the paste behaves under stress during the printing process.
Thixotropy, a specific rheological behavior, refers to the property of certain fluids to become less viscous under applied stress. In the context of solder paste, this means it becomes fluid enough to be printed through stencils but then thickens to hold its shape once the stress (like the squeegee’s movement) is removed.
Overmixing or mixing under high shear conditions, as seen in some automated mixers, can permanently alter the paste’s viscosity and thixotropy. This can lead to issues such as slumping or spreading of the paste on the board, which can cause defects in the solder joints.
Pitfalls of Automated Mixers
Because of the complexity and balance in most solder paste formulations, it’s important to understand how mixing methods impact its properties. Automated mixers, often perceived as efficient solutions, can pose significant risks to the integrity of solder paste due to their operational mechanisms and effects.
High shear stress. Unlike manual methods, automated mixers apply high shear stress to the solder paste. This stress can lead to a phenomenon known as shear thinning. In this state, the paste becomes excessively fluid, negatively impacting its ability to retain shape and form reliable joints.
Temperature changes. The operation of automated mixers can generate a considerable amount of heat, leading to an increase in the temperature of the solder paste. Note that some sources suggest this heat generation is a benefit in that it permits cold paste to reach room temperature faster, but this heat is generated by friction as opposed to natural conduction heating of paste set out at room temperature. Frictional heating can cause rises in temperature that can prematurely activate the flux or accelerate the aging of the paste, both of which are detrimental to its performance.
Inconsistent mixing across formulations. Automated mixers might not achieve uniform mixing across all solder paste formulations, particularly those with varied particle sizes or compositions. This lack of uniformity can result in unpredictable solder paste performance, with some areas of the paste potentially having different properties than others.
Perceived benefits are often illusory. Many automated mixer manufacturers emphasize the speed of preparation along with the uniformity of the paste after mixing. It’s important to note, however, that the state of the paste after mixing is not the same as the state of the paste after being idle for a while or during a print pause. This is because the forces involved in mixing cause a combination of changes to the paste’s rheological properties. Some of these changes are temporary and sustained only in the immediate aftermath of those extreme forces. (Other changes are permanent, but not in a good way – such as partial flux activation or solder sphere deformation.)
The Evidence: Real-World Implications of Automated Mixing
While empirical studies directly linking the use of automated mixers to solder paste performance issues are limited, a wealth of anecdotal evidence and professional experiences paints a clearer picture of their potential impact.
Many process engineers and technicians have reported challenges with solder paste performance that correlate with the use of automated mixers. In contrast to automated mixing, manual or proprietary mixing methods, which prioritize precision and control, have consistently demonstrated their ability to maintain the quality of solder paste.
Furthermore, there are instances where reverting from automated to manual mixing methods has resulted in observable improvements in solder paste performance. The consensus among many experts is that while automated mixers offer convenience and uniformity in preparation, they lack the nuanced control necessary to preserve the delicate balance of solder paste properties.
Mixers Used During Solder Paste Manufacturing
It’s important to note that manufacturers of solder paste do not use simple hand mixing techniques. Instead, they utilize proprietary blending processes that cannot be considered analogous to any blending done by automated mixers to prepare paste for use in an electronics production setting.
In contrast, these mixers are calibrated to ensure stable temperatures and consistent mixing, factors that automated mixers often lack. Every part of the process is carefully measured and refined and kept consistent from one batch to another, ensuring the paste produced is uniform and meets all the required specifications. The paste made in this way is also thoroughly tested after blending to further ensure it maintains its intended properties.
Best Practices for Solder Paste Preparation
The best practices for solder paste preparation involve a careful and controlled approach, with a strong emphasis on manual techniques and strict adherence to manufacturer guidelines. By following these practices, electronics manufacturers can ensure the solder paste retains its intended properties, leading to better quality and reliability in the final electronic assemblies.
Manual mixing: A preferred approach. One of the key best practices in solder paste preparation is the use of gentle, manual mixing methods. Techniques such as lightly stirring the paste with a plastic spatula for a minute or more can be highly effective. Permitting the paste to reach ambient temperature before mixing is also essential, as it ensures the paste’s properties are not altered by sudden temperature changes.
Avoiding mixers for paste warming. Using mixers to warm solder paste directly from refrigerated storage is not recommended. This practice can cause uneven heating and potentially damage the paste’s properties. Instead, the paste should be allowed to gradually come to room temperature in a controlled environment.
Adherence to manufacturer guidelines. Manufacturer guidelines are often based on extensive research and understanding of each formulation’s tolerance to different mixing methods. Look for each manufacturer’s specific instructions on the amount of time and type of mixing tool to use, ensuring the best possible performance of their product.
Automated mixers are often marketed for their ability to provide consistency in preparation and save time. Manufacturers of these mixers tout benefits such as airtight containers to reduce oxidation and humidity concerns, automated operation for even and gentle softening of the paste, and the capability to prepare paste for printing in significantly less time. These features can be particularly attractive in high-volume production environments where time efficiency is a critical factor.
What mixer manufacturers tout and what happens on the production line can be significantly different, however. While embracing innovation is key in the electronics manufacturing industry, it’s crucial to balance it with traditional practices that have proven effective, particularly in the context of solder paste preparation. While some formulations might tolerate automated mixing, others may demand the gentle and controlled environment of manual mixing. It’s essential to recognize these differences and choose the mixing method that aligns best with the specific requirements of the paste in use.
For those who choose to use automated mixers, conduct thorough testing to understand the impact of the mixer settings on the solder paste and its overall performance. Testing should include assessing changes in the paste’s viscosity, rheology and thixotropy after mixing, as well as evaluating the solder joints produced for quality and reliability.
In conclusion, while the innovation represented by automated mixers offers certain advantages, it is essential to weigh these against the proven effectiveness of traditional mixing methods. Balancing these two approaches, while staying informed about the specific needs of different solder paste formulations, is key to achieving high-quality and reliable results in electronics assembly.
Gayle Towell is content specialist at AIM Solder (aimsolder.com); gtowell@aimsolder.com.