The Importance of Design Constraints
Create them in the front end and push them into the back.
Designing today’s complex printed circuit boards is no easy task. Meeting electrical and physical design requirements can be daunting as you attempt to address layout solvability, performance and manufacturability so that version one works. Unraveling the design requirements and successfully inputting them as design constraints is key to achieving success in printed circuit board (PCB) design, as the design constraints are the rules that govern the entire design of the PCB from an electrical and physical perspective. Setting up constraints according to the design requirements as received better enables you to use automation to your advantage during the layout phase. Design constraints enable you to design quality into the PCB rather than checking for quality after the fact – and designing faster with better quality is the ultimate goal.
First, let’s understand the power and advantage of establishing and using constraints when designing PCBs. Design constraints can be created and entered either during the creation of the schematics (at the front end) or in the PCB layout (at the back end). The best practice methodology is to create them in the front end and push them into the back end. It’s important to note that the flow of how they are governed and annotated is bidirectional between the front and back end. It’s up to the designer to establish and control the flow regarding which direction of the annotation has priority over the other.
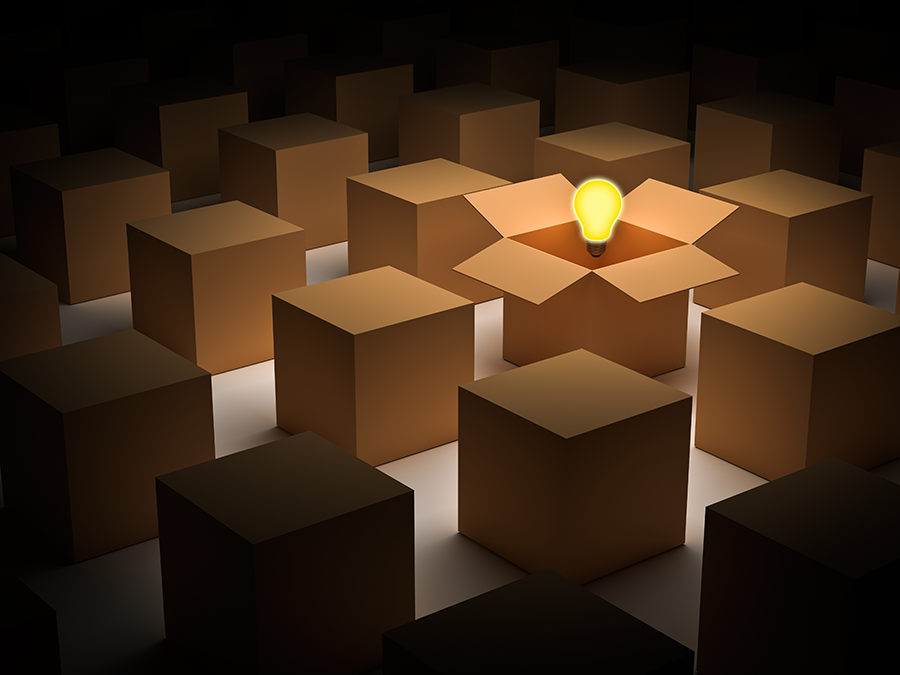
Setting up design constraints can range from a simple task to a very complex and exhausting task depending on the complexity of the design intent. Knowing the time and diligence spent upfront establishing the design constraints pays off significantly during the actual layout effort. Within the design constraints manager tool, the rules that govern the electrical and physical details of the design can be controlled and established.
A few examples of details that can be controlled are the PCB stackup, trace spacing, trace width, layer trace length/delay matching and differential pair assignments. Once the design constraints are validated and locked in, they can be exported and reused in other designs, similar to other reusable items in the library function. As electronic components become smaller and more sophisticated, PCB design constraints become increasingly crucial. Let’s explore the key constraints that designers must understand and employ to ensure success in the PCB design process.
The first key to success in PCB design is designing for layout solvability, especially regarding size and form factor constraints. Miniaturization and sleek designs are the trends in electronic devices. Designers face the challenge of fitting an increasing number of components into smaller spaces while maintaining optimal functionality. Form factor constraints dictate the physical size and shape of the PCB, impacting the overall dimensions of the end-product. Component placement will dictate the quality of the routing. The arrangement of components on the PCB and the routing of traces plays a crucial role in the overall performance of the circuit. Designers must optimize component placement to minimize signal paths, reduce noise and ensure efficient signal flow.
The second key for success in PCB design is to design for the performance of the PCB, specifically regarding signal integrity, electromagnetic interference (EMI), power integrity and thermal management. Design constraints play a key role in solving for this. Maintaining signal integrity is paramount for the proper functioning of electronic devices. Factors such as impedance matching, signal propagation delay and crosstalk must be carefully managed. Designers need to consider the type of signals, transmission lines and routing techniques to ensure the reliability of data transmission. Adding to this is power distribution. Efficient power distribution is critical for the reliable operation of electronic components. By utilizing design constraints, designers must balance the power requirements of different components, manage power plane distribution and minimize voltage drops to prevent performance issues and ensure stability. Addressing thermal management is a part of this perspective that cannot be overlooked. As electronic components become more powerful, heat dissipation becomes a significant concern. Thermal constraints involve designing effective heat sinks, ensuring proper airflow and placing components strategically to prevent overheating, which can impact performance and lifespan.
The third key to success in PCB design is designing for manufacturability. PCB designs must be manufacturable at scale and within budget constraints. Highest yield at the lowest cost is the goal. When creating and implementing design constraints, designers need to consider factors such as manufacturability of components, assembly processes, and the choice of materials to ensure cost-effective and efficient production. Knowing and understanding the engineering decisions made at the point of design and how they will affect downstream activities in manufacturing is vital in the quest for PCB design success.
Industry regulatory compliance must also be considered when creating design constraints. Compliance with industry standards and regulations is nonnegotiable. Designers must be aware of regulatory requirements related to EMI, electromagnetic compatibility and safety standards to ensure that the final product meets legal and safety guidelines. Industry standards and guidelines such as IPC specifications provide helpful guidelines for PCB design.
In the ever-evolving landscape of electronic design, understanding the importance of PCB design constraints is crucial. Balancing the technical requirements with practical considerations is a continuous challenge for designers. By utilizing design constraints, you’re better enabled to design quality into the board rather than simply checking for it after the fact.
Stephen Chavez is a senior printed circuit engineer with three decades’ experience. In his current role as a senior product marketing manager with Siemens EDA, his focus is on developing methodologies that assist customers in adopting a strategy for resilience and integrating the design-to-source Intelligence insights from Supplyframe into design for resilience. He is an IPC Certified Master Instructor Trainer (MIT) for PCB design, IPC CID+, and a Certified Printed Circuit Designer (CPCD). He is chairman of the Printed Circuit Engineering Association (PCEA); stephen.chavez@siemens.com.