Investigating Intermittent Soldering Defects
Resolving solder issues requires an examination of the entire process.
by Timothy O’Neill
The PCB assembly process creates millions of solder joints with great precision, which is why intermittent soldering defects can be particularly frustrating. It is common to assume that soldering materials, such as solder paste and flux, are the primary cause of these issues. But is solder always to blame?
In this article, we explore a real case study and shed light on the importance of accurate diagnosis and vendor collaboration.
A common misconception is that if there is a solder defect, the soldering materials are at fault. Fortunately, solder paste is not an intelligent entity capable of selectively causing defects. Solder paste is, in essence, a passive material that follows the instructions given to it during the assembly process.
Soldering defects can stem from several factors, including equipment setup, environmental conditions, component characteristics, and handling processes. Therefore, thoughtful examination of the entire soldering process is essential. This includes scrutinizing the printer setup, pick-and-place issues, reflow oven performance, and other relevant parameters.
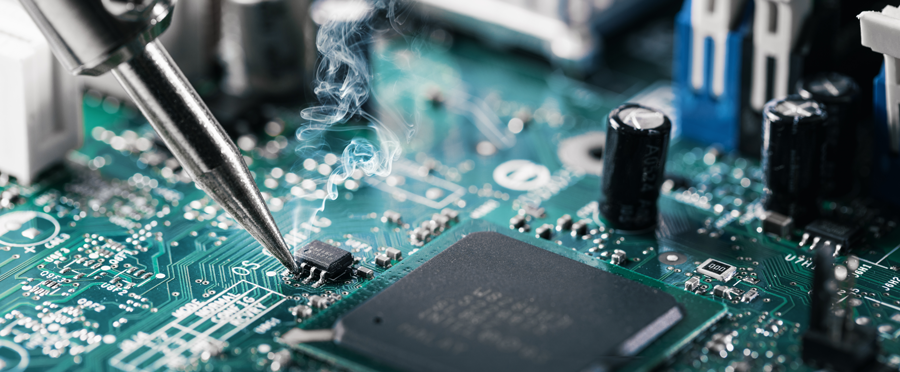
Case Study: Intermittent Solderability Issues
In the following scenario, a PCB assembler encountered a problem with intermittent solderability of a specific component in the PCB assembly line.
The intermittent nature of the issue made it particularly frustrating. At times, the solderability problem would arise, causing disruptions, but it was repairable at the rework station. While this did not completely halt production schedules, it created extra work, wasted time, and raised concerns about the overall quality of the assemblies.
Attempts to diagnose the issue involved multiple visits from the solder supplier’s field engineer. Each time the engineer was present, however, the issue did not present itself, leaving the team at a loss. These instances highlighted the difficulty in diagnosing intermittent problems and the complexity involved in root cause analysis.
Investigation Checklist
The following checklist can help guide the initial investigation process:
- Screen printer setup:
- Check that the screen printer is level and plumb.
- Ensure screen printer rails are parallel to one another and the floor.
- Verify the correct tooling is in place.
- Thoroughly examine equipment cleanliness.
- Inspect the stencil condition for any damage or clogging.
- Pick-and-place process:
- Ensure cleanliness of the pick-and-place machine’s nozzles.
- Ensure no contamination is affecting the pick-and-place process.
- Verify the placement settings are optimized for the assembly and components.
- Reflow oven performance:
- Check for malfunctions in the heating elements of the reflow oven.
- Inspect the blower motors for any issues.
- Verify with a profiler that the reflow oven is functioning properly.
If these factors are ruled out, attention can be directed to other contributing inputs. In the aforementioned case study, these basic factors were examined, but none was identified as the source of the intermittent solderability issue.
Examining Components, Environment and Process Settings
The next step is to examine the characteristics and behavior of any components involved in the problem, as well as environmental factors and process settings.
Internal handling refers to how a component is stored, handled, and transported within the manufacturing facility. The goal is to identify any possible mishandling and then correct it.
Environmental factors, such as temperature and humidity variations, particularly in regions with extreme climates, can affect the soldering process. In the case study, the production environment was adequately controlled. And while the facility experienced seasonal variation in temperature and humidity, these conditions were not correlated with the solderability issue.
Reflow profile optimization involves fine-tuning the reflow process to accommodate specific assembly thermal characteristics. By optimizing the reflow profile, issues such as residue relocation, solder void elimination, and improved wetting can be addressed. In the case study, the reflow profile was optimized by an SMTA-certified engineer using the latest profile data collection techniques. This optimization ensured that the reflow process was within recommended parameters.
Wetting balance testing is used to determine component solderability. However, the test cannot simulate a reflow profile and cannot detect subtle solderability issues that may occur during a three to five-minute SMT reflow profile. In the case study, wetting balance tests conducted by the component vendor did not indicate any defects, highlighting the need for additional investigation.
Rapid application of high-temperature solder during wetting balance tests may reveal gross solderability issues but can also break down oxides present on the component, unintentionally masking defects that may emerge during the longer, hotter reflow profile. Moreover, the reflow process can exacerbate oxide formation before soldering occurs, potentially worsening any issues.
To overcome these limitations, customer-supplied components were subjected to baking at 125°C for five minutes, mimicking the exposure to reflow. After this treatment, the components were subjected to wetting balance testing.
The results of the bake process were immediately apparent – the components did not solder correctly after exposure to elevated temperatures. This testing was repeated on multiple component lots, and each time, the same solderability issue was observed, consistent with the behavior experienced at the customer’s site. The evidence allowed the assembler to present the component vendor with clear and undeniable information, compelling them to address the issue and provide a remedy.
Vendor Collaboration
Resolving soldering issues can be challenging, often complicated by conflicting advice from multiple vendors involved in the PCB assembly process. This can leave manufacturers feeling uncertain and overwhelmed.
It is crucial to recognize that vendors play a pivotal role in addressing soldering issues effectively. They possess valuable expertise, insights, and product knowledge that can contribute to finding solutions. Rather than perceiving conflicting advice as a hindrance, it should be approached as an opportunity to engage in meaningful collaboration and problem-solving.
Commitment, patience and vendor support are key when it comes to resolving soldering issues. Choosing vendors who actively support their products and are committed to assisting with customer processes is a smart decision that can lead to effective resolution.
Timothy O’Neill is director of product management at AIM Solder (aimsolder.com); toneill@aimsolder.com.