Water Quality Matters
A novel approach leverages ion exchange technology with continuous monitoring for superior tank management.
by Christopher T. Riley
Aqueous cleaning operations in printed circuit board population require particular attention to water quality. Various soils – internal and external to the population processes – need to be removed to a very high degree to ensure trouble-free operation of the circuit board. The water used for the makeup of the cleaning solutions and rinsing must also be of very high quality to minimize the potential for contamination of the circuit board, with ion exchange technology being the technology of choice to purify and recover the water.
The quality of printed circuit boards, their operating characteristics, and ultimately, their lifespan depend on several factors, with one of the more important factors being the cleanliness of the boards. Several soils, if not removed, can negatively impact the operation of circuit boards. Incomplete removal of solder flux residue, for example, can lead to corrosion and potential short circuits. Aqueous cleaning chemicals may contain various additives (such as saponifiers, surfactants, etc.) that aid in soil removal but must also be completely removed from the PCB, as failure to remove these cleaning chemicals can lead to the formation of residual spotting on the board.
Water, used for aqueous cleaning chemical makeup, as the cleaner itself, or for rinsing, is a critical component of the circuit board cleaning process. The water must be clean enough so that it does not leave any residue on the board after the cleaning process. City water typically contains background ions, such as calcium, magnesium, sodium and potassium that, if not removed (along with corresponding ions such as chloride, nitrate, phosphate and sulfate), can deposit and cause spotting or otherwise leave residue on a board after drying. Removal of these background ions before using the water in the PCB cleaning process is imperative to obtaining a contamination-free (or as close as possible) product.
Water Quality
Water quality for board cleaning operations is typically expressed in terms of conductivity, resistivity or total dissolved solids. Conductivity is the ability of the water to conduct electricity and is usually expressed as “microsiemens/centimeter” or “ìS/cm.” Resistivity, or the ability of the water to resist conducting electricity (and the inverse of conductivity), is typically expressed as “Megaohm-centimeter” or “MΩ-cm” – commonly abbreviated as “megohms.” Total dissolved solids (TDS) is a measure of the total number of ions in solution and is normally expressed as “milligrams per liter” or “mg/L” or “parts per million,” or “ppm.” To relate these terms to the measurement of water quality, quality increases (contaminant concentrations decrease) as conductivity and TDS decrease and as resistivity increases; an example of this is shown in Table 1.
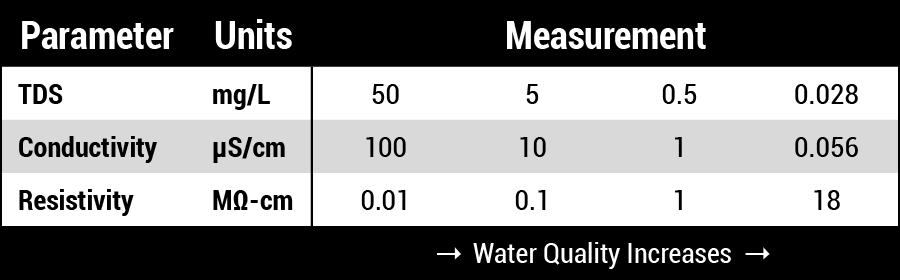
Since the purpose of cleaning and rinsing PCBs is to remove soils and minimize residual contaminants – including those from the water itself – it makes sense that higher-quality water is required. Water quality requirements vary – sometimes greatly – for board cleaning applications, typically ranging from 1MΩ-cm to 18MΩ-cm.
Water Treatment Processes
Several common treatment processes are employed to increase the quality of water used to clean PCBs. These processes include filtration (removing particulate or suspended solids), softening (removing hardness from calcium and magnesium), carbon treatment (to remove organic compounds), reverse osmosis (removing virtually all divalent and most monovalent cations) and deionization (removing all ionic components). Which processes are employed depends on the characteristics of the water requiring treatment as well as, typically, the size of the required water treatment system.
Of the treatment technologies listed, only deionization, most often achieved using ion exchange technology, can achieve the required water quality of greater than 1MΩ-cm. Neither filtration nor softening reduce the TDS, and reverse osmosis (RO) can only partially remove TDS – but not to the level typically required for RO alone to be used as a means of deionization. Filtration, carbon adsorption and RO are, however, often used as pretreatment for ion exchange treatment.
Ion Exchange Technology
Ion exchange technology uses polymeric beads that have been functionalized to remove either cations (positively charged ions such as calcium or Ca+2) or anions (negatively charged ions such as sulfate or SO4-2). Processing water through a bed of mixed cation exchange resin and anion exchange resin (a “mixed bed”) results in the removal of essentially all the charged species in the water and can produce water quality up to 18MΩ-cm.
Ion exchange is a mass-loading-limited technology in that the resin has a finite exchange/loading capacity that, when reached, must be replenished through regeneration or replacement. This finite capacity also means that the throughput – how long the resin lasts in the service cycle – is directly related to the concentration of ions in the feed water. The lower the ionic concentration (lower TDS) in the feed water, the longer the resin lasts in service.
Ion exchange technology is deployed either through a service or as a fixed system at the end user’s site. In the service deployment, tanks of ion exchange resin and activated carbon are leased by the end-user and, when depleted, returned to the supplier for regeneration and processing. In the fixed system, tanks of ion exchange resin are fixed in place at the end user’s facility and regenerated in place, necessitating the storage, use and treatment/disposal of acid and caustic chemicals.
Ion Exchange Treatment for PCB Wastewater
PCB cleaning may generate two types of wastewaters – a dilute rinsewater and a more concentrated cleaning waste. Ion exchange technology is well suited to the treatment of the dilute circuit board cleaning rinsewater, either for removing regulated metals (such as lead) to meet discharge limits or to recover the water for use back in the process or elsewhere in the facility.
PCB cleaning rinsewaters are especially attractive for recovery/reuse given their typically low TDS levels. One also must be cognizant of the organic content of the rinsewater (typically measured as total organic carbon, or TOC), as well as the suspended solids (typically measured as total suspended solids, or TSS) as both types of contaminants can greatly impact the successful recovery of rinsewater to the required quality.
A typical ion exchange system used to recover circuit board cleaning rinsewaters consists of:
- Cartridge filtration to remove TSS (dirt, dust, debris, solid flux residue)
- Activated carbon to remove dissolved TOC (cleaner and flux components)
- Mixed bed ion exchange resin to remove TDS (cationic and anionic elements).
An example of a typical ion exchange water recovery system is represented in Figure 1.
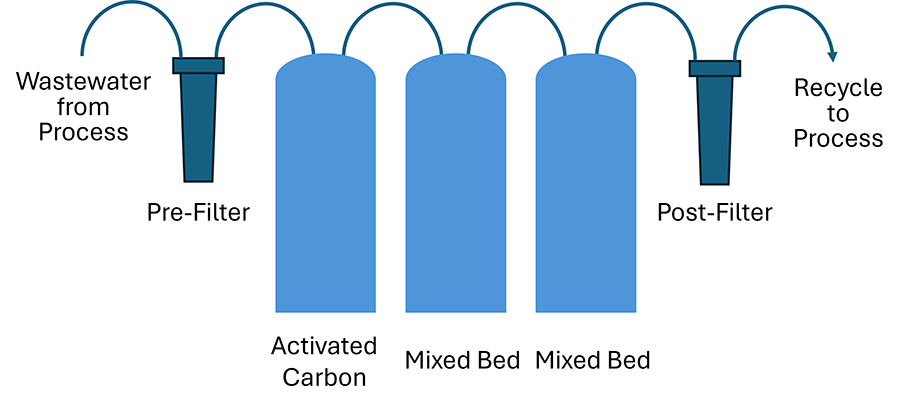
Smart Technology to Maintain Recovered Water Quality
Typical ion exchange wastewater recovery systems are set up in a worker-polisher (two mixed bed tanks in series) configuration and monitored manually, with treated water quality being measured with either in-line resistivity monitors or “quality lights.” The resistivity monitors provide a resistivity number directly (or convert mathematically to TDS) while the quality lights show “green” if the resistivity is above the light’s setpoint or “red” if it is below the light’s setpoint. Based on these readings, in a service exchange system, tank changes are initiated by the user notifying the supplier that a tank change is required. Another option typically employed is to change tanks on a timed basis, before they are spent, regardless of the monitoring results – the assumption being that maintaining recovered water quality outweighs the cost of changing tanks before they are spent or exhausted.
A novel process, called Water One WX, combines traditional service wastewater ion exchange with remote monitoring and data logging capabilities. The system, monitored 24 hours per day by a centralized control center, measures several key wastewater performance parameters including flowrate, feed water conductivity and resistivities from both the worker- and polisher-mixed bed exchange tanks. When the worker-mixed bed quality drops below the specified setpoint, an alarm is sent to the control center who then initiates an exchange of the mixed bed tank with the supplier’s service network. Before the tank exchange, the “polisher” tank ensures that the ion exchange system is providing the necessary water quality required for the cleaning process while relieving the end user of routine monitoring activities and responsibility to initiate tank exchanges.
The novel system, shown in Figure 2, does more than track ion exchange effluent quality. In addition to the water quality parameters previously noted, the system also measures and logs feed water temperature and differential pressure across cartridge filters while also monitoring the system for leaks. Alarms are also sent for negative deviations from these parameters which will trigger service events.
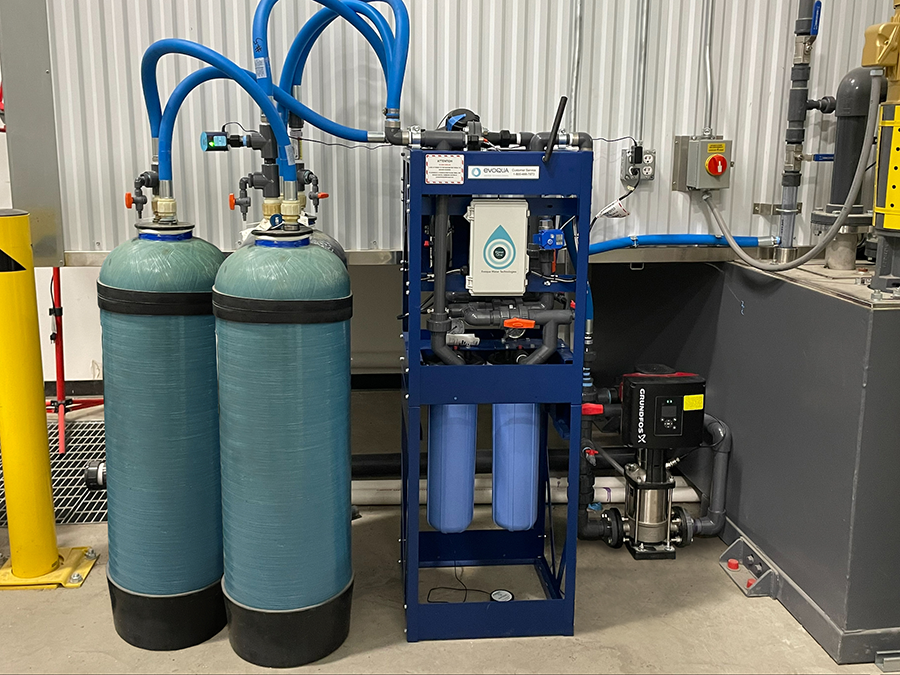
The novel unit compiles the water quality data collected, and the predictive analytics estimate the consumption of the worker mixed bed and forecast the remaining tank capacity. The historical data, including the performance cycles of previous mixed bed tanks, are stored and can be retrieved for evaluation and comparison to support user facility audits and to assist any troubleshooting efforts. All the relevant operating data are accessed via the unit’s dashboard, with a typical dashboard view shown in Figure 3.
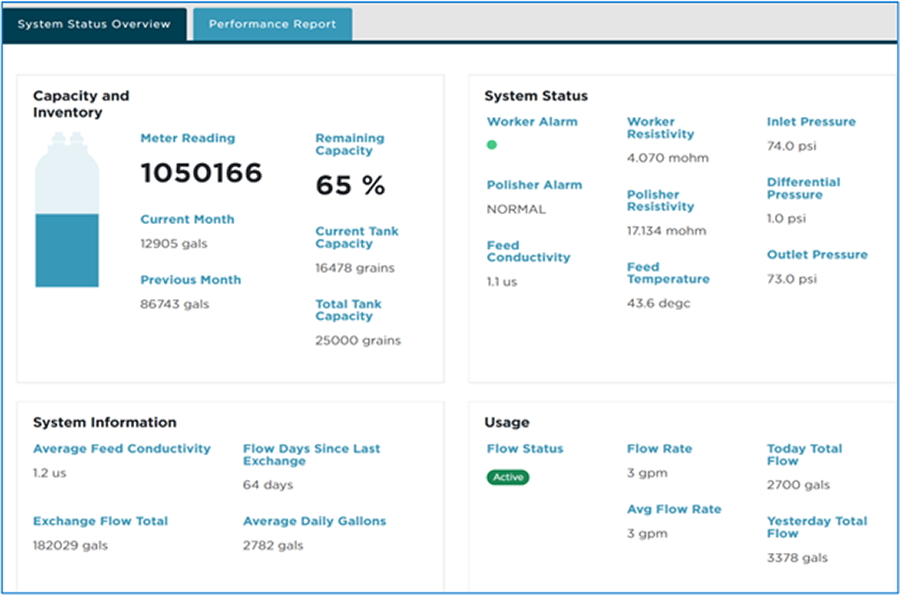
Case Study Examples
A microelectronics components manufacturer required high-quality rinsewater, greater than 16MΩ-cm, for cleaning its flexible circuit boards. A service-based ion exchange system was installed consisting of cartridge filtration, activated carbon and mixed bed ion exchange resin. The system was monitored manually, using a system of quality lights, with tank changes initiated by the customer when the quality lights indicated that a change was necessary. The system was converted to the novel system, which relieved the customer from both monitoring tank effluent quality and calling in for required tank changes. Between the remote monitoring and subsequent identification (and elimination) of a regular – but previously unknown – conductivity spike (captured by the system as shown in Figure 4) caused by a cleaner discharge into the system, mixed bed tank usage was reduced by 30% on an annual basis while maintaining the quality necessary for the company’s process.
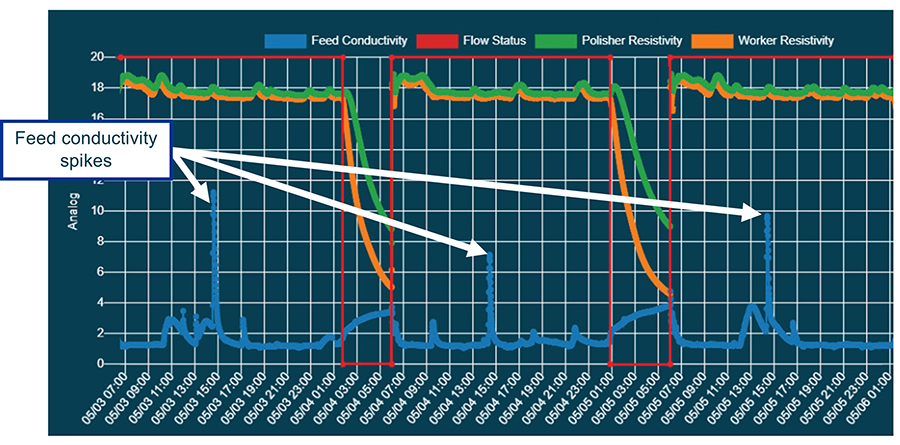
Another manufacturer and assembler of rigid PCBs installed a similar ion exchange system to treat and recover the rinsewater from its finished circuit board washing process. In this application, tank monitoring was initially minimized by performing regular mixed bed tank exchanges based on time, which ensured that the recovered water quality was maintained but did not utilize the full capacity of the ion exchange resin. The system was converted to the novel system, and the resulting continuous monitoring permitted the required recovered water quality to be maintained while reducing annual mixed bed tank usage by 33% and relieving the customer of the time and effort of monitoring the water quality and calling in for tank changes.
Conclusion
Printed circuit board operation and lifespan is directly related to its cleanliness. The cleanliness of the PCBs is in turn directly related to the quality of water used for cleaning and rinsing. Ion exchange is a mature technology for producing and recovering high-quality, clean water for this process. A novel system takes the well-established technology of service ion exchange and couples it with remote monitoring of key water quality parameters to maximize usage of the ion exchange resin and minimize the need to monitor and maintain the system while maintaining required water quality for the process – allowing the user to minimize any concern about recovered water quality and concentrate on its core business.
Chris Riley is technical services director for the Wastewater Ion Exchange (WWIX) business at Evoqua Water Technologies, now part of Xylem (evoqua.com); christopher.t.riley@evoqua.com.